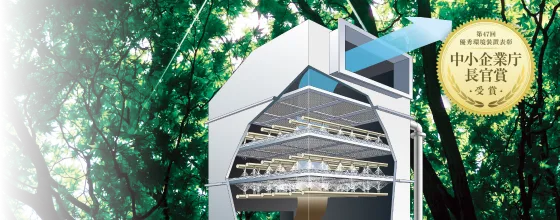
他の湿式スクラバー(脱臭・排ガス処理装置)とはここが違う!「デオライザー」4つの特長
1 臭いと埃をキャッチ
水膜により、さまざまな臭気物質はもちろん、微細粉塵も確実にキャッチします。
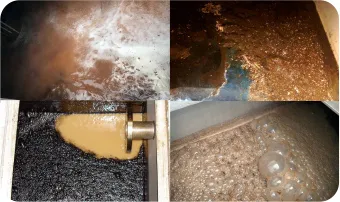
2 水の膜で捕捉
スクリーンに水膜を形成し、気液接触効率100%を実現しています。
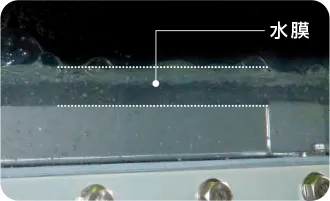
3 メンテナンスが簡単
従来型湿式スクラバーに比べ、大幅にランニングコストが低減されます。
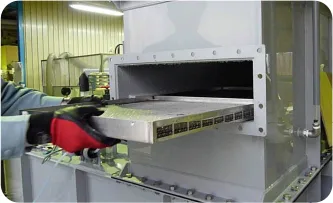
4 スラッジの発生を抑制
散気装置「アクアブラスター」を搭載。水の腐敗を防止し、スラッジの発生を抑制します。
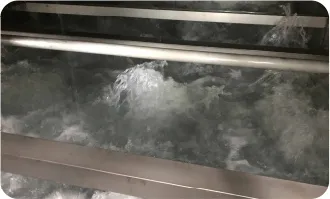
地球環境にやさしく高性能な湿式スクラバーです。
1. 臭気成分と微細粉塵を捕捉
ニオイとホコリを確実にキャッチします。
2. 水膜で100%気液接触
40mm前後の水膜で、排ガスをシャットアウト。
3. カートリッジ式スクリーン採用
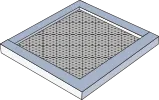
50cm角のスクリーンで、楽々交換。
4. アクアブラスター内蔵
水の腐敗を防止し、循環水の長期利用を可能にしました。
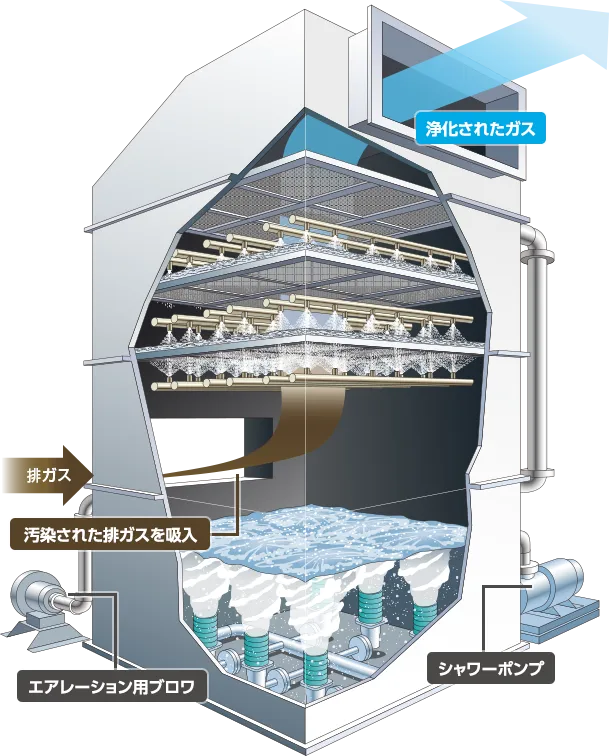
これまでの脱臭概念を変えた、
脱臭・排ガス処理装置「水膜式スクラバーデオライザー」。
水膜なので高い気液接触効率を誇り、確実に臭気成分を捕捉します。
また、タンク内に散気管アクアブラスターを搭載し、捕捉した有機物を生分解することで、
循環水の腐敗やスラッジの発生を抑制し、循環水の長期クローズ化を実現しました。
「水膜式スクラバー デオライザー」はこれまでの水洗スクラバー式脱臭機の欠点を一掃した、次世代の超高性能集塵排ガス処理装置です。
驚きの捕捉力! 他の湿式スクラバー(排ガス処理装置)と比べてみてください。
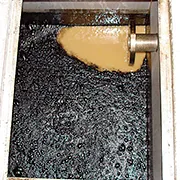
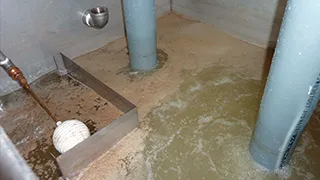
たった数時間でこれだけ捕捉しました
他とはココがちがう!
- 「水の膜で捕捉」だから、ニオイ・ホコリを確実にキャッチ!
- 「カートリッジ式接触材」だから、簡単メンテナンス
- 「高性能散気管 アクアブラスター搭載」だから、スラッジの発生を抑制し水が腐敗しません!
洗浄式排ガス処理装置 水膜式スクラバー「デオライザー」の特長
スクリーンに水膜を形成することで
高い気液接触効果を発揮
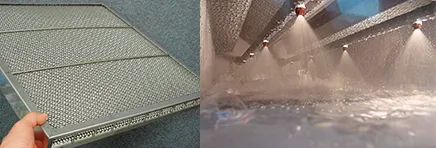
カンタンカートリッジ交換式

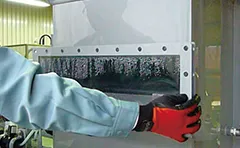
閉塞しにくく圧力損失が変わりにくい
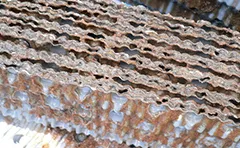

水の腐敗を防ぎ、汚泥が発生しにくい
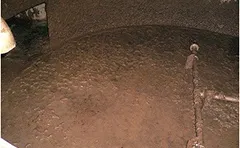
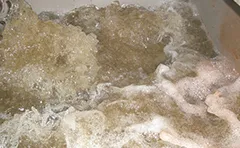
水膜式スクラバー(脱臭・排ガス処理装置)「デオライザー」は
さまざまな工場の臭気物質に、幅広く対応いたします。
脱臭方式の種類と適用業種 ○適用、 △条件付きで適用、 ×不適用
脱臭方式の種類 | 印刷工場 | 塗装工場 | 鋳物・鋳造 | 化学工場 | 食品工場 | 製紙パルプ | 繊維工場 | 下水・ゴミ | 飼料・肥料 | 飲食店 | |
燃焼方式 | 直接燃焼方式 | △ | △ | △ | △ | △ | △ | △ | △ | △ | × |
---|---|---|---|---|---|---|---|---|---|---|---|
蓄熱式燃焼方式 | ○ | ○ | △ | △ | △ | △ | △ | △ | △ | × | |
触媒式燃焼方式 | ○ | ○ | △ | △ | △ | △ | △ | △ | △ | × | |
吸着方式 | 固定床回収方式 | ○ | △ | △ | ○ | △ | △ | △ | △ | △ | × |
流動式回収方式 | ○ | △ | △ | ○ | △ | △ | △ | △ | △ | × | |
ハニカム式濃縮方式 | ○ | △ | △ | ○ | △ | △ | △ | △ | △ | × | |
交換式吸着方式 | ○ | △ | △ | ○ | △ | △ | △ | △ | △ | × | |
洗浄方式 | 水 | △ | △ | △ | ○ | ○ | ○ | ○ | ○ | ○ | ○ |
酸・アルカリ | △ | △ | △ | ○ | ○ | ○ | ○ | ○ | ○ | △ | |
酸化剤 | △ | △ | △ | ○ | ○ | ○ | ○ | ○ | ○ | △ | |
※ | デオライザー | △~○ | ○ | ○ | ○ | ○ | ○ | ○ | ○ | ○ | ○ |
生物脱臭方式 | 土壌脱臭方式 | △ | △ | △ | △ | △ | △ | △ | ○ | △ | × |
スクラバー式脱臭方式 | △ | △ | △ | ○ | ○ | ○ | ○ | ○ | ○ | × | |
充填塔式脱臭方式 | △ | △ | △ | △ | ○ | ○ | ○ | ○ | ○ | × | |
曝気式脱臭方式 | △ | △ | △ | △ | △ | △ | △ | ○ | △ | × |
水膜式スクラバー(脱臭・排ガス処理装置)「デオライザー」による臭気削減率表
物質名 | 物質濃度削減率 | 水への溶解度 | 中和 | 通過風速 | |
窒素化合物 | アンモニア | ○ | 54g/100ml | 要 | 0.75~1.0 m/sec |
---|---|---|---|---|---|
トリメチルアミン | ○ | 108g/100ml | |||
ジメチルアミン | ○ | 23.7g/100ml | |||
ジエチルアミン | ○ | 完全溶解 | |||
硫黄化合物 | メチルメルカプタン | ○ | 2.3g/100ml | 要 | 0.75~1.0 m/sec |
硫化水素 | ○ | 0.67g/100ml | |||
硫化メチル | ○ | 知見なし | |||
二硫化メチル | ○ | 知見なし | |||
アルデヒド類 | ホルムアルデヒド | ○ | 完全溶解 | 不要 | 0.5~0.75 m/sec |
アセトアルデヒド | ○ | 任意で溶解 | |||
プロピオンアルデヒド | △~○ | 22g/100ml | |||
ノルマルブチルアルデヒド | △~○ | 知見なし | |||
イソブチルアルデヒド | △~○ | 11g/100ml | |||
イソマルバレルアルデヒド | △~○ | 知見なし | |||
イソバレルアルデヒド | △~○ | 知見なし | |||
イソブタノール | △~○ | 8.7g/100ml | |||
VOC | 酢酸エチル | △ | 8.7g/100ml | 不要 | 0.5m/sec以下 |
メチルイソブチルケトン | △ | 1.8wt% | |||
トルエン | ×~△ | 不溶 | |||
キシレン | ×~△ | 不 溶 | |||
スチレン | ×~△ | 30mg/100ml | |||
イソプロピルアルコール | ○ | 完全溶解 | |||
メチルエチルケトン | △~○ | 29g/100ml | |||
ホルムアルデヒド | ○ | 完全溶解 | |||
酢酸プロピル | △ | 2.3wt% | |||
シクロヘキサン | ×~△ | 不 溶 | |||
フェノール | △~○ | 8.4g/100ml | |||
PGME | ○ | 完全溶解 | |||
PGMEA | ○ | 20g/100ml | |||
Nメチル-2-ピロリドン | △~○ | 知見なし | |||
アセトン | △~○ | 任意溶解 | |||
メタノール | ○ | 任意溶解 | |||
エタノール | ○ | 任意溶解 | |||
脂肪酸 | プロピオン酸 | △~○ | 知見なし | 要 | 0.5~0.75 m/sec |
ノルマル酪酸 | △~○ | 知見なし | |||
ノルマル吉草酸 | △~○ | 知見なし | |||
イソ吉草酸 | △~○ | 知見なし |
※数値はスクラバー デオライザーによる平均的削減率を記載しておりますが、原臭濃度によっても異なりますので、参考値とお考えください。
実際の現場で実験機による脱臭デモを行いご確認いただくことをおすすめ致します。
どうして水膜が必要なのか?
ミクロの世界をのぞいてみると…
ネット式充填材の幅は約2mm、隙間が約5mmです。ミクロの世界で考えてみると、臭気物質が1~5ミクロンで、それを叩き落とす水滴が約150ミクロン。これを1000倍すると、臭気物質が1~5mm、水滴が150mmのソフトボールくらいになります。そして充填材の幅は2m幅の小道、隙間はなんと5mにもなり、気液接触率が悪いことが判ります。
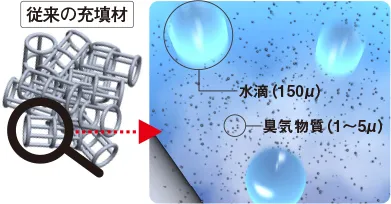
気液接触メカニズム
アンモニア(NH₃)ガス量300m³/min、550ppm→5ppm(90%削減)した場合の設計比較表
備考 | 従来型湿式スクラバー | デオライザー | |
液体(L)/ガス(G) | ガス量に対して液量が多いほど気液接触効率は高くなります。 | 530L/min/300m³/min L/G=1.7 ※水は循環使用かワンパス | 1960L/min/300m³/min L/G=3.2 ※水は循環使用 |
充填材厚み | 充填材は閉塞しにくく、メンテナンスが簡便であることが重要です。 | 1,700mm ※閉塞を起こす | 40mm×2層 ※ほとんど閉塞しない |
圧力損失 | 圧力損失が低いほうがファンの電気容量も少なくエネルギー効率が良くなります。 | 700mmAq ※閉塞により圧損増加 | 800mmAq ※圧損は変わらない |
水膜式スクラバー(脱臭・排ガス処理装置)「デオライザー」に標準装備された画期的な特殊積層式ステンレス製スクリーン
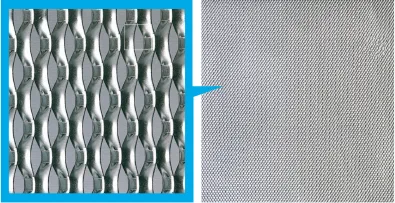
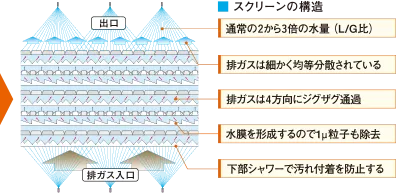
処理方式見極めフロー図
※有機溶剤は、FRP・PVCを溶かすことがあります。
※デオライザーを含めて、100点満点の脱臭方式はありません。しっかりと処理方式を見極めていただき、「消去法」で選んでいただくことを推奨させていただきます。
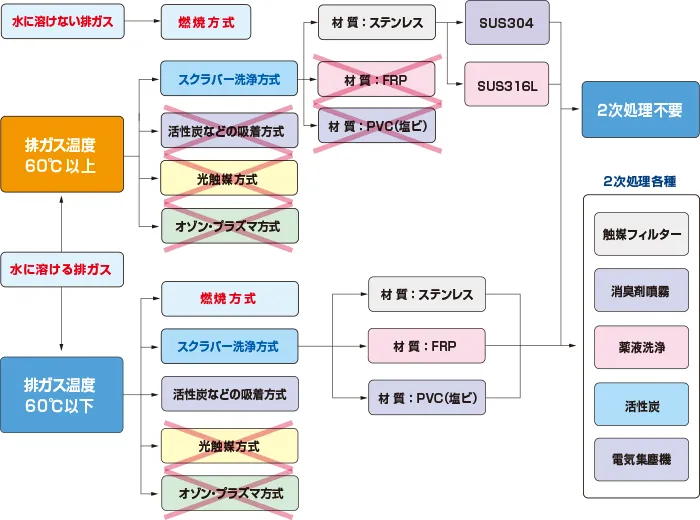
現地でデモ実験を行うことが可能です。
どのポイントでご満足いただけるか、デモで明確にすることで、さまざまなリスクが解消されます。
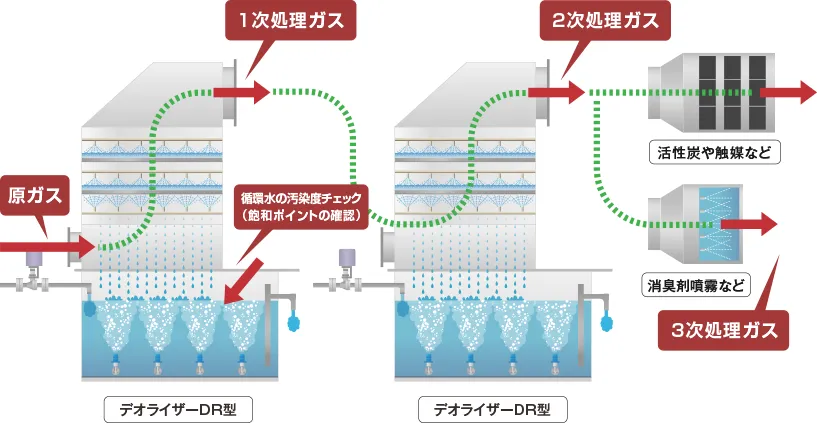
イニシャルコスト差があっても、
ランニングコストで1~2年で逆転します
方式 | デオライザー | 充填式スクラバー | |
![]() | ![]() | ||
比較仕様 | ガス流量 | 500m³/min | |
---|---|---|---|
ガス温度 | 30℃ | ||
圧力 | 大気圧 | ||
イニシャルコスト | 4,000万円 | 3,000万円 | |
耐用年数 | 20年以上 | 10年 | |
ランニングコスト | 電力費:12円/kw (年間稼働4800h/年時) | 20kwh×12円/kw×4,800h = 1,152,000円/年 | 20kwh×12円/kw×4,800h = 1,152,000円/年 |
イニシャルコスト | 40,000,000円/10年 = 4,000,000円/年 | 30,000,000円/10年 = 3,000,000円/年 | |
点検整備 | 最大事例で 50万円/回 × 2回 = 1,000,000円/年 (お客さまでもメンテナンス可) | 200万円/回 × 3回 = 6,000,000円/年 | |
接触材交換期間 | 30分 (緊急対応可) | 3日 (緊急対応不可) | |
10年間のコスト総額 | 61,520,000円 | 101,520,000円 |
最短2年、最長でも8年でコスト逆転し、
10年以降大差が生じます。
スクラバー(排ガス処理装置)「デオライザー」・充填式スクラバー 累計コスト比較
イニシャルコスト差: 1,000万円、メンテナンスコスト差: 500万円の場合
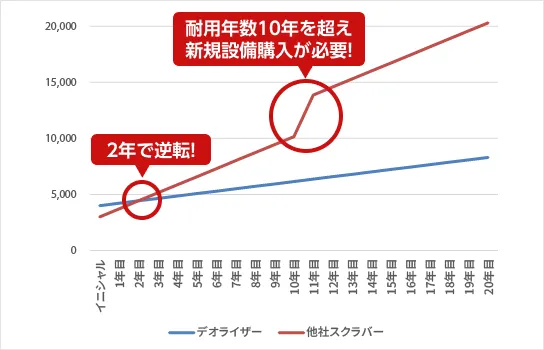
メンテコスト | 電力 | イニシャル | 1年目 | 2年目 | 3年目 | 4年目 | 5年目 | 6年目 | 7年目 | 8年目 | 9年目 | 10年目 | 11年目 | 12年目 | 13年目 | 14年目 | 15年目 | 16年目 | 17年目 | 18年目 | 19年目 | 20年目 | |
デオライザー | 100 | 115 | 4,000 | 4,215 | 4,430 | 4,645 | 4,860 | 5,075 | 5,290 | 5,505 | 5,720 | 5,935 | 6,150 | 6,365 | 6,580 | 6,795 | 7,010 | 7,225 | 7,440 | 7,655 | 7,870 | 8,085 | 8,300 |
---|---|---|---|---|---|---|---|---|---|---|---|---|---|---|---|---|---|---|---|---|---|---|---|
他社スクラバー | 600 | 115 | 3,000 | 3,715 | 4,430 | 5,145 | 5,860 | 6,575 | 7,290 | 8,005 | 8,720 | 9,435 | 10,150 | 13,865 | 14,580 | 15,295 | 16,010 | 16,725 | 17,440 | 18,155 | 18,870 | 19,585 | 20,300 |
イニシャルコスト差: 2,000万円、メンテナンスコスト差: 300万円の場合

メンテコスト | 電力 | イニシャル | 1年目 | 2年目 | 3年目 | 4年目 | 5年目 | 6年目 | 7年目 | 8年目 | 9年目 | 10年目 | 11年目 | 12年目 | 13年目 | 14年目 | 15年目 | 16年目 | 17年目 | 18年目 | 19年目 | 20年目 | |
デオライザー | 100 | 115 | 4,000 | 4,215 | 4,430 | 4,645 | 4,860 | 5,075 | 5,290 | 5,505 | 5,720 | 5,935 | 6,150 | 6,365 | 6,580 | 6,795 | 7,010 | 7,225 | 7,440 | 7,655 | 7,870 | 8,085 | 8,300 |
---|---|---|---|---|---|---|---|---|---|---|---|---|---|---|---|---|---|---|---|---|---|---|---|
他社スクラバー | 400 | 115 | 2,000 | 2,515 | 3,030 | 3,545 | 4,060 | 4,575 | 5,090 | 5,605 | 6,120 | 6,635 | 7,150 | 9,665 | 10,180 | 10,695 | 11,725 | 11,210 | 12,240 | 12,755 | 13,270 | 13,785 | 14,300 |
水膜式スクラバー(排ガス処理装置)「デオライザー」循環水の処理方式
1.セットリングタンク浄化方式
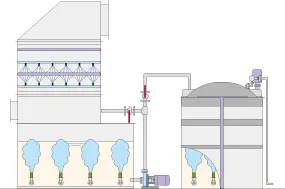
循環使用後の水を、別置きのタンクに移して少量ずつ水処理を行う方式。例えば、5トンの循環水が3ヶ月間使用できたとすると、5トン÷90日で、日量55リットルの水を処理すればよく、排水処理設備に負荷をかけなく、希釈放流も可能。
2.水処理装置併設方式
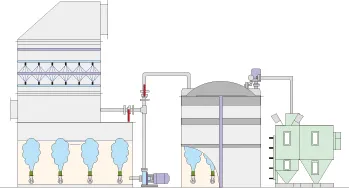
アイエンス製ユニットタンクを併設し、定期的に浄化して放流する方式。循環水の程度によっては、油水分離装置や凝集装置なども併用する。排水処理や下水道設備のない事業所に向く。
3.下水放流方式
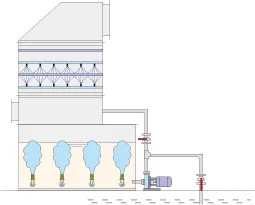
下水放流基準値以内で循環水を適時に放流していく方式。最初に数回のデータ測定をして、下水放流基準値をオーバーするまでの使用期間を調べる必要があるが、その後は非常に手間のかからない方式。
現場 | 循環水交換の目安 |
塗装乾燥炉排ガス処理 | 1~4ヶ月 |
化学工場排ガス処理 | 1~4ヶ月 |
食品工場排ガス処理 | 1~4ヶ月 |
飲食店排ガス処理 | 3~6ヶ月 |
4.産業廃棄方式
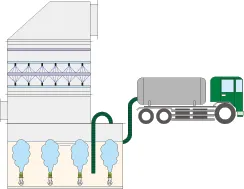
循環水を使用できる限界まで連続使用し、産廃処理する方式。ゼロエミッションには反するが、排水処理や下水道設備のない事業所に向く。5トンの循環水を5ヶ月使用し1トンあたりの処理費が35,000円とすると日コストは、1,170円とリーズナブル。
5.定量注水方式
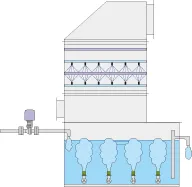
電磁弁で調整しながら、定量の補給水を注水して、循環水をオーバーフローさせることで、常に放流基準値以内の水を排出する方式。主に、地下水など、水が安価に使用できる事業所に適する。
水膜式スクラバー(脱臭・排ガス処理装置)「デオライザー」
標準仕様規格表
型番 | DR-1W | DR-2W | DR-4W | DR-6W | DR-9W | DR-12W | DR-16W | DR-20W | DR-24W | DR-30W |
処理風量(m³/min) | 1~13 | 13~26 | 25~50 | 40~80 | 60~120 | 75~150 | 100~200 | 130~260 | 160~320 | 200~400 |
本体圧力損失 | 通常運転時 800Pa (設計時 1100Pa) | |||||||||
---|---|---|---|---|---|---|---|---|---|---|
ポンプ出力/60Hz(kw) | 1.5 | 2.2 | 3.7 | 5.5 | 7.5 | 7.5 | 11.0 | 11.0 | 15.0 | 18.5 |
ブロワ出力/60Hz(kw) | 0.53 | 0.53 | 0.88 | 2.10 | 2.10 | 2.80 | 3.60 | 3.60 | 3.60 | 6.30 |
横幅(mm) | 1,050 | 1,400 | 1,400 | 1,400 | 2,000 | 2,000 | 2,480 | 3,000 | 2,686 | 3,050 |
奥行(mm) | 2,300 | 2,300 | 2,300 | 2,470 | 2,640 | 3,145 | 3,145 | 3,300 | 4,060 | 4,100 |
高さ(mm) | 2,591 | 2,591 | 3,605 | 3,755 | 3,790 | 4,155 | 4,155 | 4,155 | 4,355 | 6,124 |
乾燥重量(kg) ポンプ・ブロワ・外部配管除く | 550 | 850 | 1,150 | 1,450 | 2,700 | 3,250 | 3,950 | 4,200 | 5,350 | 5,900 |
※余儀なく設計変更する場合があります。
※シャワー洗浄部と循環水タンクをセパレートにすることも可能です。
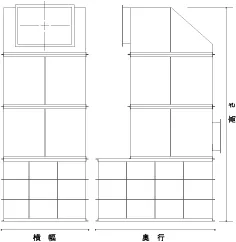